Installation qualification (IQ), operational qualification (OQ), and performance qualification (PQ), better known as IQ OQ PQ, is an important quality assurance (QA) process. This process is most often found in highly regulated industries where quality is essential for consumer safety. This includes industries like food and beverage, pharmaceuticals, medical devices, aerospace, and other highly regulated areas.
Putting this process in place in an organization can be complicated but it will pay dividends by helping to ensure your company produces safe, good quality products and stays compliant with industry regulations.
To help better understand what IQ OQ PQ is, the challenges around implementing it, and why you need it, we’ve put together a shortlist of several factors you should know about the QA practice. Here are five fast facts about IQ OQ PQ.
1. It is critical in regulated industries
The industries listed above, and others, are regulated by the government because the products each produces have a high chance of causing harm to the user if they become ineffective or go bad. Additionally, consumers generally can’t see the difference between a bad piece of food, pill, or airplane part and a good one. Without quality assurance regulations, there is no way of knowing a product has been produced the right way.
Much goes into QA in these industries. IQ OQ PQ is one process that happens right from the start. This process allows producers to incorporate new processes and equipment and makes sure they will produce the desired results before the equipment comes online. When IQ OQ PQ is performed correctly, it forms a solid foundation for the entire production process.
2. It is often required for compliance
There are plenty of good reasons to implement IQ OQ PQ into your QA processes but the most important reason, in many cases, is that it is required for compliance in many industries. In several industries, such as the food and beverage and pharma industries, the Food and Drug Administration makes this QA process mandatory.
Failure to create an IQ OQ PQ program can result in problems for an organization. If the governing body that requires this process finds the program is not up to par or is not being followed, heavy fines can be leveled or the whole enterprise can be shut down until the situation is remedied.
Even in situations where IQ OQ PQ isn’t required, it is just good practice. In situations where it is required for compliance, it must be done right to avoid negative consequences.
3. It can be expensive
Although IQ OQ PQ is a vital QA process, it is not a cheap one. Doing this right requires a serious capital investment. It takes experts who know how to qualify equipment and systems. Hiring these types of people can be pricey. Also, it is an ongoing process that requires new qualifications all the time.
In business, where time is money, a time-consuming process like IQ OQ PQ can be a major budget-suck. If you don’t have enough experts on staff to do the qualification quickly and efficiently it can lead to costly delays. If you use employees who aren’t full-time IQ OQ PQ experts, it also takes a great deal of time away from their other responsibilities which will cost the organization money in the long-term as well.
4. It helps to have expert help
Because IQ OQ PQ is time-consuming and needs to be performed by trained experts, it makes sense to bring in outside help for this process. IQ OQ PQ is an ongoing process but it is not a constant one. There may be times when you don’t need these types of experts on staff but when you do they become very important.
This is why having these specialized professionals on staff is tricky for many organizations. They cost a lot of money to hire full-time and when they’re not performing IQ OQ PQ, they may have to perform less valuable tasks. When they are working on qualification, it is an all-consuming task so other responsibilities go out the window.
The good news is, you can partner with specialized firms to handle IQ OQ PQ when you need it. This gives you the highest level of expertise when you need them and you don’t have to pay for anyone when you don’t. It also helps avoid mistakes in this process by using someone who may know about IQ OQ PQ but isn’t a specialist.
5. Getting it wrong has major consequences
The last thing you need to know about IQ OQ PQ ties into all the other points above. If you don’t implement this process or don’t do it the right way, there can be major consequences for an organization.
Getting IQ OQ PQ right means having a plan, using the right experts to execute that plan, and staying committed to this valuable QA process. The consequences of not doing so are immense.
In industries where IQ OQ PQ is part of compliance, we’ve already discussed that fines or even shutdowns can be a consequence of poor QA. That’s not the worst thing that can happen, though, with poor IQ OQ PQ.
The worst-case scenario is that the QA process fails and a company puts ineffective or unsafe products into the world. If the product fails and hurts someone or even many people, the consequences can be devastating. Fines, PR hits, reputation damage, lawsuits, and more can follow and have a serious negative effect on a company or even force it out of business.
To help get a better idea of what doing IQ OQ PQ right looks like, you need to know more about each step of the process and what are the best practices for each one. This Dickson guide is a useful resource for some best practices pertaining to IQ OQ PQ.
Conclusion
IQ OQ PQ is a critical quality assurance process and if your industry requires it, or you just want to ensure you have the best products possible, it is worth implementing. Performing it correctly is crucial, so finding the right expert partners should be a top priority.
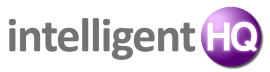
Founder Dinis Guarda
IntelligentHQ Your New Business Network.
IntelligentHQ is a Business network and an expert source for finance, capital markets and intelligence for thousands of global business professionals, startups, and companies.
We exist at the point of intersection between technology, social media, finance and innovation.
IntelligentHQ leverages innovation and scale of social digital technology, analytics, news, and distribution to create an unparalleled, full digital medium and social business networks spectrum.
IntelligentHQ is working hard, to become a trusted, and indispensable source of business news and analytics, within financial services and its associated supply chains and ecosystems